Pulsed Light Sterilization
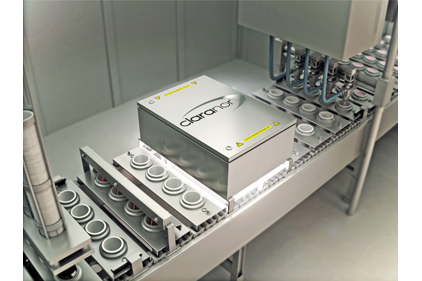
The first trials using intense light flashes for surface decontamination date back to the 1980s. The first patent was taken out in 1984 in Japan by Hiramoto for the use of xenon lamps.
The literature from 1990-2000 describes many trials carried out on a wide range of food items on the laboratory level. Most of these articles failed to specify the physical parameters of the trials.
Hence the results could not be linked to cost elements, which have held back the technology from reaching the industrial market.
That’s why the first industrial applications for online packaging treatment began in the early 2000s.
Physical principle
The technology of pulsed light is based on the bactericidal effect of intense flashes of white light generated by xenon lamps.
Energy is accumulated in a capacitor, and a high-voltage signal sparks an arc. This arc sets off a flash of intense luminosity, which only lasts a few microseconds and covers the entire white light spectrum (but is particularly rich in UV rays).
Action on microorganisms
The performance of the technology in destroying microorganisms on surfaces has been explained by:
• The effect of UV rays, which have a denaturation effect on the DNA of microorganisms,
• The high power of the flash (short time, high energy).
The technology’s efficacy has been demonstrated on a wide range of microorganisms, such as bacteria (vegetative cells and spores), moulds, yeasts and viruses.
In view of the low energy levels needed to generate the flashes, pulsed light has been classified in the soft technologies category, along with high pressure and pulsed electric fields. Among these technologies, pulsed light stands out on account of its demonstrated efficacy in destroying thermo-resistant spores.
Decontamination levels attained depend on the number and power of the flashes applied to a surface. They can vary from a single log reduction to total sterilization.
Pulsed light is a surface technology—only the areas reached by the flash light, directly or by reflective phenomena, are decontaminated. Shadow effects, linked to the shapes of the objects treated, constitute the limit of the technology.
Applications
Consumer demand for fresher food produce has made it necessary to modify industrial transformation methods. Some processing steps induce a surface recontamination hazard. In these cases, treatment with pulsed light can secure the product’s shelf life without modifying its properties. Since its discovery, the efficacy of pulsed light has been tested on a wide range of applications at laboratory level. However, the industrialization of the technology has so far been possible only for packaging material sterilization.
Closures, cups, films and preforms used in the food and beverage industry can be treated with a pulsed light unit integrated on the packaging line for ultraclean and extended shelf life products.
Trials on food product surfaces (bread and cakes, meat and seafood, vegetable and fruit, etc.) and on transparent liquids have also yielded positive results.
Present day, several technical centers are conducting research projects on these topics.
For more information on pulsed light applications for
Claranor—rise of a Cleantech
Claranor is an independent company established in 2004 and controlled by its founders and a number of investors.
After measuring decontamination levels greater than log 6 reduction on bacterial spores inoculated on plastic surfaces under laboratory conditions, Claranor focused its development on packaging material treatments.
In fact, the France-based company was the first to succeed in proposing industrialized pulsed light equipment with performances that replace chemical methods used in the food processing industry.
As a world leader in applying pulsed light to packaging sterilization, Claranor invests heavily in research and development with a view to developing reliable applications that suit the needs of the food and beverage industries.
The near future should see the launch of pulsed light solutions complying with aseptic requirements, such as shelf-stable products.
Fields of expertise and organization
All Claranor equipment is built in Claranor-owned and operated workshops. All of the skills necessary for handling each project from start to finish have been brought together by:
• Knowledge of the packaging-related hygiene issues.
• Mechanical and optical engineering, including use of IT tools specifically developed for modeling machine components.
• A qualified production team for equipment assembly, including power electronics parts and on-site installation and maintenance.
• A microbiology department that supervises the qualification of industrial projects and new applications in collaboration with an independent laboratory.
Fowler Products, powered by Pro Mach, manufactures high-performance capping machinery and cap-feeding systems. Fowler Products is based in Athens, Ga., and can be reached via its website at www.fowlerproducts.com.
Looking for a reprint of this article?
From high-res PDFs to custom plaques, order your copy today!