Automated Warehousing Systems—Are They for You?
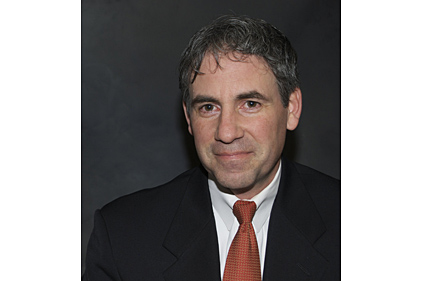
The human body isn’t designed to work in sub-zero temperatures, yet the majority of frozen food operations conduct warehousing activities manually, requiring workers to physically withstand harsh environments. This is not only risky for the worker, but also the operation as a whole. With workers taking frequent, but necessary “warm-up” breaks and the need to move product out of the freezer and into a more favorable environment for picking, the organization is quick to realize inefficiencies in time, labor and energy usage.
In order to combat these inefficiencies, today’s most forward-thinking food operations are turning to automation technology to decouple labor from sub-zero environments. While there are many benefits of an automated storage/retrieval system (AS/RS), such as improving productivity and increasing inventory accuracy, many companies are hesitant to make the investment. Why? Often, companies deem automation too expensive or too large of an undertaking. Or, companies are putting off the inevitable investments due to the need to achieve short-term goals. Simply put, they are intent on the quick fix rather than on the long-term solution that will allow for a clear competitive advantage.
Despite the preconceptions about automation technology, it is simple to decide whether an AS/RS system for freezer applications is the right investment by taking the following 3-fold approach. First, perform an analysis of the warehousing system’s existing design and framework. Then, examine some basic, yet key criteria to determine if the operation is suited for automation technology. And, finally, justify the basic cost for such a system by demonstrating its overall benefits.
Data analysis and metrics
Data analysis is the first step in determining the requirements of any frozen food warehousing and distribution operation. Answering the following five questions will help build a sanity check using basic data that should be easily available:
1. How much inventory (in pallet positions, if appropriate) must be stored in a given design year (ex: five years out)?
2. How many items (SKUs) does the inventory comprise? This should include all variations of product size, container type, etc.
3. How many SKUs represent approximately 80% of the annual sales volume and 80% of the inventory? (Pareto analysis)
4. How many unit loads per hour enter and exit the warehousing operation? Warehouse input could be from production and/or outside suppliers. Outbound loads could be full pallet to truck or replenishments to a pick area.
5. How many hours or shifts is the warehousing operation active?
Knowing this information and ensuring its accuracy are crucial to form an initial idea of whether or not warehouse automation is a good fit. Let’s put this information to work.
1. The capacity of the system will define the cube of the warehouse. Most automated systems storing finished goods tend to have more than 500 pallet positions of storage. Systems smaller than that tend not to be candidates for automation.
2. The number of SKUs will define how selective the inventory will have to be, thus enabling the potential use of multiple deep systems, which reduces the building footprint.
3. The pareto analysis (80/20 rule) will validate what SKUs have the volume and inventory, allowing you to allocate the right storage depth to the right type of inventory.
4. The throughput will determine the number of storage/retrieval machines (S/RMs) needed. Throughputs less than 20-30 pallets per hour total will tend to be more difficult to justify.
5. The number of working hours will determine whether the asset will be used for more than one shift. Automated systems used in single shift operations tend not to be justifiable. Two shift operations tend to be more justifiable.
Dig deeper into data. Is automation the right fit?
By analyzing the inventory data in more detail, you can determine the average inventory levels per SKU and divide these into logical groups. The following breakdown groups can be used as a guideline:
· Inventory levels per SKU of less than seven pallets—use single-deep storage.
· Inventory levels per SKU of 8-14 pallets—use double-deep storage.
· Inventory levels per SKU of 15 and greater—use multiple-deep storage.
By defining these conditions, it is possible to gauge if the operation is best suited for single-deep or multiple-deep storage. With multiple-deep storage, considerable space savings are achieved, but selectivity is reduced. Therefore, you generally want to store the same SKU in a multiple-deep storage lane. Automated systems have an advantage in that they can automatically re-warehouse pallets, as long as this work is not performed during peak shipping hours.
Most manufacturing operations that store frozen products are candidates for multiple-deep storage because, typically, a small number of items account for 80% or more of the volume and inventory. So, how deep (storage lane depth) should they store their inventory? Again, this depends on the inventory levels per SKU. Generally, "high inventory item SKUs," or items with more than 30 pallets per SKU, are assigned to a storage block, which is anywhere from 7-12 pallets deep. The rest of the items are assigned to another storage block, which ranges from 2-6 pallets deep. Of course, with automated systems, each lane at every level is accessible. Compared to a drive-in or drive-through rack, it is obvious that an 8-deep automated high-density warehouse will result in a higher storage utilization than a 4-deep, 3-high drive-in rack system serviced by conventional fork trucks. In the automated case, to get to the eighth pallet, seven pallets must be removed. In the conventional case, to get to the last three pallets, nine pallets must be removed.
Perhaps the most important statistical information concerns throughput. In conventional systems, throughput determines the staffing levels and the number of fork trucks required, whereas with automated systems, throughput determines the quantity of S/RMs required. One S/RM is usually capable of handling between 60- to 70-unit loads per hour when handling one unit load at a time. Systems handling two unit loads at a time are also available.
Cost justification
Assuming an automated freezer is deemed to be a good fit, it is time to justify its cost by looking at the following elements:
1. Site conditions. Consider site conditions of the warehouse. If the site is landlocked, the automated system is advantageous because the building (assuming new construction) can be as high as 90-100 feet (although 40-80 feet is more typical). This reduces the slab size, and can allow the storage facility to remain on an existing property. If an existing building is to be retrofitted with automation, increases in density can often achieve 30-50% more storage.
2. Labor requirements. Calculate the labor required to operate the facility. As mentioned before, freezers are difficult places to work and require frequent warm-up breaks. Worker productivity in environments with automation technology is often significantly higher.
3. Inventory accuracy and control. Look at inventory accuracy and the level of control needed to manage it. Do employees requiring inventory management information know what is on hand and where it is located at all times? An automated system ensures accurate inventory control on a real-time basis.
4. Equipment shifts. Lastly, assess the number of shifts the equipment is running per day. Typically, automated systems require a 2-shift operating period. This is logical, as any machinery must be properly utilized to be justifiable.
Perform the justification of an automated system using discounted cash flow capital budgeting techniques. When using straight payback methods, the time value of money is rarely taken into account. To compound the problem, the benefit of having the automated system operate for its anticipated life of more than 25 years is ignored. Fortunately, determining the net present value (NPV) and the internal rate of return (IRR) is easy with today’s spreadsheet programs. These figures should indicate if there is an appreciable justification for the initial cost difference associated with installing an AS/RS vs. building a conventional system. Compare both of these by establishing cash flow differentials, and then apply the cost differential to the cash flow benefits.
Final considerations
Automated systems for freezer applications have clear advantages over conventional systems. In addition to reducing the overall footprint and cube, which can lead to building cost reductions, AS/RS technologies offer many long-term benefits, including increased productivity, enhanced inventory accuracy and control and reduced energy costs. These attributes will position your company for growth and profitability.
Looking for a reprint of this article?
From high-res PDFs to custom plaques, order your copy today!