The Latest FSMA Proposals and Impacts on the “Cold Chain”
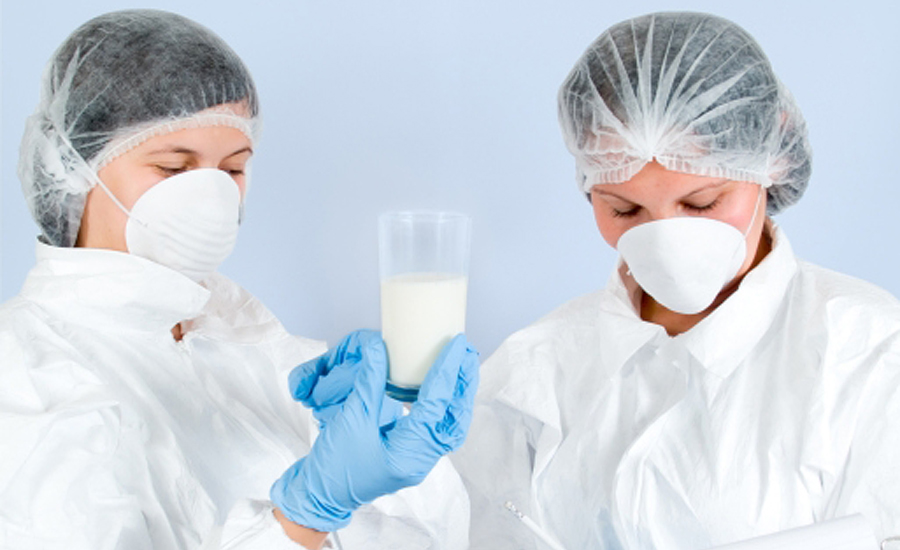
With the Food & Drug Administration’s latest comment period for changes to the Food Safety Modernization Act set to expire Dec. 15, it behooves the “cold chain” to examine proposals set forth. Food safety for consumers is a key aspect of the act, but the burden of compliance needs to be equally shared and the complexities of the supply chain better understood by the regulators enforcing the law.
Two components of the proposed produce safety regulation could potentially have a significant impact on the supply chain—water quality testing and raw manure use. Under the water testing component, farmers who don’t meet microbial standards during initial testing will have more options for meeting the benchmark. The regulation would also allow for a tiered approach to testing based on contamination risk.
As for manure use, the FDA is reviewing the required time interval between when farmers apply raw manure to fields and when they can harvest the crops.
It’s all about reassuring customers that there’s a slim chance their fruits and veggies will become contaminated with bacteria, especially among smaller producers. In doing so, however, brings additional costs associated with implementing the new standards, increases testing and augments record keeping. More complex testing and preventive measures can also lead to slowdowns in production.
The proposed regulations around preventive controls for human and animal foods would require more extensive testing on both products and the facilities themselves, as well as supplier controls. Some corporations have already implemented these types of controls in feedlots. Organic and local farmers that feed their own animals will likely experience the greatest impact.
As with the produce safety regulations, the preventive controls are intended as customer reassurance. Each link within the supply chain will be expected to provide more complete track and traceability. Producers with feedlots on their grounds must conduct additional testing to make sure they’re meeting food safety and increased nutritional requirements.
All of that could have a trickledown impact on refrigerated and frozen food distributors, who might experience thinner profit margins as producers pass along some of the extra costs. Distributors might incur their own additional costs if they have to adjust warehouse processes to keep in step with the regulations. The time producers devote to meeting the new standards could also result in interruptions in distribution and decreased customer satisfaction.
Smaller and even mid-market producers have historically been more reactive to many regulations than their larger counterparts, but these shifts will force them to abide by a more proactive mindset. They’ll either have to pay now to get in line with regulations, or pay later in the form of hefty fines. Aside from potential fines, a company’s reputation can suffer irreparable damage if its product causes an outbreak of foodborne illness, say from microbes in irrigation water.
Technology can often help minimize the costs associated with adapting to new regulations. Warehouse management systems (WMS), for example, deliver capabilities like freshness tracking and proactive alert notifications, and can help large and small distributors alike manage the complexities of the law.
Food producers can learn a lot from the pharmaceutical industry, which is also in the midst of beefing up track-and-trace requirements. Free information exchange among suppliers, shippers and receivers will be hugely important under the new rules. And, cloud technology, for instance, can make it easier to share, link and exchange data about temperatures throughout a product’s journey.
The refrigerated and frozen food industry has a reputation for meeting its supply chain challenges head-on. The latest FSMA proposals can, and will be, addressed through thoughtful consideration of the most efficient, safe and cost-effective ways to store and transport goods.
Looking for a reprint of this article?
From high-res PDFs to custom plaques, order your copy today!