Moving Transport Refrigeration Forward
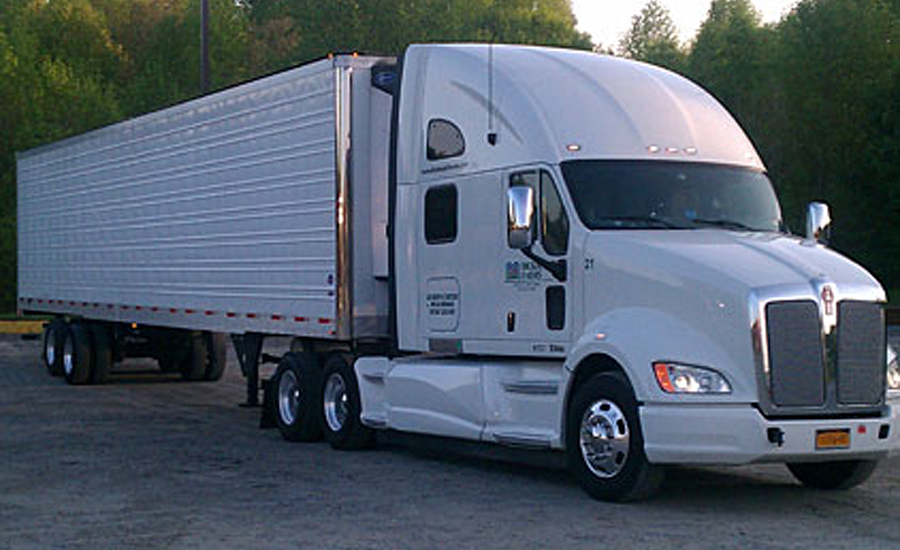
The globalized agricultural and food processing industry offers U.S. consumers year-round access to a wide variety of food products grown in diverse climates and growing conditions. But, transporting those temperature-sensitive products—from fruits and vegetables to meats, seafood and frozen foods—through drastically varying climates and environments presents a huge challenge to the world’s food chain both in terms of engineering and regulatory compliance.
The transportation equipment and HVACR systems responsible for maintaining precise interior conditions during transit play a critical role in ensuring that food arrives in the same condition and with the same level of quality as when it left the field, factory or warehouse. And yet as important as these systems are, they are in a state of constant change. These systems carry products across international borders, causing manufacturers to respond to a variety of complex regulations, including foreign policies such as the European Union’s Fluorinated Gas (F-gas) legislation, a key driver for the industry-wide transition to low global warming potential (GWP) refrigerants. The U.S. EPA’s Tier 4 regulations governing diesel engine emissions represents another example of regulations impacting the U.S. transportation sector.
Today’s transport refrigeration industry is under immense pressure to engineer solutions that not only meet layered global regulatory standards, but also the environmental challenges of safely moving perishable products around the globe throughout the year.
Challenges today, opportunities tomorrow
Transport refrigeration is one of the most demanding segments in commercial refrigeration. The same refrigerated container, commonly referred to as a reefer container, that brings fresh strawberries into the country from Mexico in January might turn around immediately and ship American beef across the Atlantic to Europe. These refrigeration systems need to manage loads of varying sizes and types while dealing with exposure to harsh environmental conditions, ranging from sweltering desert heat to the corrosive salt of ocean swells. Extreme ambient temperatures can cause interior temperatures to spike, posing a serious risk to food freshness and safety and significantly affecting fuel efficiency. This application demands extremely high levels of engineering capable of simultaneously managing these competing concerns and helping to deliver high-quality foods at competitive prices.
One of the forces driving these technological advancements is EPA’s Tier 4 emissions standards for diesel engines. Tier 4 standards began in 2011 and are to be phased in completely during 2015. These standards require manufacturers to produce new engines that reduce levels of particulate matter (PM) and nitrogen oxides (NOx) to levels 50-96% lower than those of the existing generation of diesel machines. Tier 4 regards transport refrigeration systems as “off-road” engines, the same categorization as construction equipment that includes large earthmoving machines. It also requires these engines use only ultra-low sulfur diesel fuel, which contains no more than 15 ppm sulfur and which has been standard for on-road diesels since 2006.
These standards, while seemingly routine, are in fact transformational for the transport refrigeration industry. Diesel engines, particularly those used in off-road applications, are uniquely durable, often lasting decades or more. Thus, beyond regulation, there is little incentive to replace existing engines with new and more efficient technologies even though some older diesel engines have 20-40 times the emissions levels of Tier 4 engines. When the Tier 4 standards were announced, manufacturers and their suppliers recognized the opportunity to build systems explicitly designed to cope with the rigors of the transport refrigeration sector.
Extreme engineering and customized performance
Unlike most commercial refrigeration applications for which many components are used interchangeably, the equipment used in transport systems is designed specifically to meet the challenges of navigating extreme conditions. With deep expertise in commercial and industrial refrigeration applications, Danfoss, a Bethpage, N.Y., manufacturer of high-efficiency electronic and mechanical components for air conditioning, heating, refrigeration and motion systems, adapted a broad portfolio of products—expansion devices, line components, pressure controls, scroll compressors, system controllers and Micro Channel heat exchangers—to specifically meet the unique needs of transport refrigeration equipment and systems.
For example, many reefer containers also utilize variable frequency drives, which optimize the control of compressors, reduce energy consumption and provide constant pressure regulation. Fewer starts and stops reduce mechanical wear, and speed control is attractive when a compressor is running for long periods at part load.
In addition to ensuring engine performance in extreme temperatures, simply maintaining system operation onboard a transoceanic shipping vessel is a critical task for the transport refrigeration sector. Filter driers, for instance, are especially vulnerable to the corrosion that can result from saltwater waves because they are located on the liquid line, which connects the outdoor engine case to the indoor unit and are typically left exposed for ease of access.
The future of transport refrigeration
Unlike stationary refrigeration systems, those involved in the food chain cross international borders, subjecting them to multiple regulations and adding a layer of complexity not seen in other applications. EPA’s Significant New Alternatives Policy (SNAP) rules, which were recently extended in October 2014 to permit the use of CO2 in refrigerated transport applications, are driving the transition to natural refrigerants with low GWP in virtually all U.S. refrigeration and cooling applications. The European Union’s F-gas regulation also is pushing the transport refrigeration segment down the same path.
By 2030, the F-gas legislation, updated on Jan. 1, seeks to reduce Europe’s global warming emissions from hydrofluorocarbons (HFCs) by four-fifths compared with average levels from 2009 to 2012 by using quotas to phase out the use of HFCs. These quotas will drive up prices of HFCs with high GWP. The legislation includes a service ban, taking effect by 2020, on the use of virgin F-gases with GWP greater than 2,500 on systems with a charge size greater or equal to 40 tons of CO2; from 2030, the service ban also will cover reclaimed refrigerant with GWP above 2,500. R404A, an HFC refrigerant traditionally used in truck and trailer cooling units, is likely to be phased out completely in all commercial applications as part of the service ban (40 tons of CO2 is equivalent to about 22.5 pounds of R404A). While most truck, trailer and van units do not possess a big enough charge to fall under the service ban and the reefer container segment commonly uses R134a, which has a GWP of 1,430 and thus is unaffected by the new regulations, manufacturers are still proactively developing technology that utilizes alternative refrigerants like R452A or CO2.
Even though the revised F-gas regulation does not explicitly prohibit the use of HFCs in transport refrigeration systems, it is having a direct effect on end users by prescribing tougher maintenance requirements. The 2015 revisions increase requirements for leak prevention, record keeping and training and certification of service technicians. For instance, unlike the 2006 rules, which were based on system charge, leak checks now depend on the amount of tons of CO2 equivalent contained in the refrigerant circuit. This mandates more leak checks for systems that use high-GWP refrigerants, effectively serving as a service tax on those units.
In addition to adapting traditional system designs for use with CO2 refrigerant, equipment manufacturers are creating innovative new systems that benefit from CO2’s unique thermodynamic properties. Anticipating the transition, Danfoss is already leading the charge and adapting much of its portfolio for use with CO2 as the refrigerant gains traction in broad refrigeration applications, including transportation.
Transport refrigeration is not a one-size-fits-all market. Rather, it’s one in which environmental challenges and regulatory changes are rapidly driving the development of technologies specially adapted to provide maximum flexibility. To keep the transport industry moving forward efficiently and the food chain developing safely, it is critical that refrigeration component and equipment manufacturers establish close partnerships to develop solutions that help the industry meet its evolving performance objectives while anticipating future demands and challenges.
Looking for a reprint of this article?
From high-res PDFs to custom plaques, order your copy today!