Decoding tubing material solutions for food, beverage dispensing
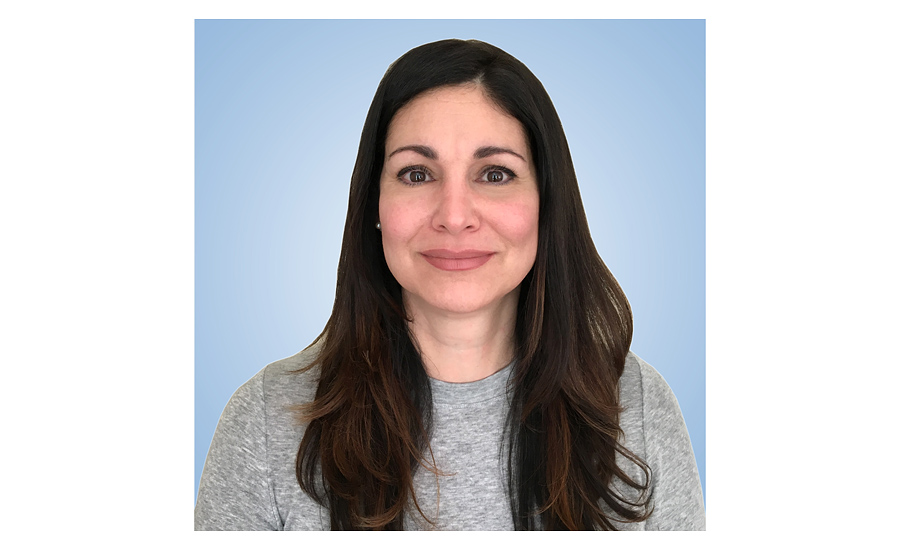
From the ubiquitous hand-pump for cheese on nachos to peristaltic pumps for ice cream and slushies, food and beverage dispensing equipment can vary. Products dispensed by this equipment also vary and include everything from dairy to juice and more. Many of these product categories also feature highly specific and often diverse characteristics. For instance, yogurt, ice cream and milk can accelerate bacterial growth on tubing surfaces if not properly sanitized with cleaning chemicals.
Therefore resistance properties, such as chemical, corrosion, abrasion and pressure – in varying degrees – are critical to the performance of food and beverage dispensing tubing as well the equipment as a whole. And, because dispensing equipment is used under varying levels of pressure as well as extreme temperatures, the durability of components is significantly important. Though a small component, dispensing tubing can have a major impact on the overall effectiveness of dispensing equipment and an operation. As a result, determining, designing and implementing the appropriate food and beverage dispensing tubing solutions is a critical step in ensuring the quality, consistency and safety of a product.
Dispensing tubing materials must be carefully selected based on criteria for the specific application to ensure the tubing performs well over its useful product lifecycle. Tubing solutions made from a variety of high-performance polymers and other enhanced materials can offer a wide range of attributes, making them ideally suited for various applications.
There are several factors to consider when specifying dispensing tubing materials. For example, tubing designed specifically for use with solvents requires special properties in the inner bore to withstand negative effects to taste, odor and product purity caused by extraction from the tubing. Dispensing equipment that utilizes a pressurized pump to dispense the product requires a different material formulated to withstand higher pressure. Often times a multi-material toolset is needed to deliver the best solution.
Below is a list of materials used in food and beverage dispensing tubing as well as their key properties.
Polyvinyl Chloride (PVC)
This material can be used for aqueous foods and dairy products, but should not be used for products with high fat or alcohol content. PVC offers sealability, high flexibility, high clarity and some moderate resistance to pressure and cleaning chemicals, but may be prone to leaching, which may impact taste/odor. With the addition of an optimized formulation type and concentration, it can offer a long pump life (50-1,000 hours).
Polyolefin-based formulations
This type of tubing can be used for aqueous foods and dairy products, but it should not be used for foods with high-fat content. Polyolefin-based formulations have limited leachables and offer a high resistance to any impact on taste/odor. However, they usually do not withstand extended dynamic deformations associated with peristaltic pumping, resulting in pump life of 25-100 hours. Nevertheless, this material offers sealability, good flexibility and moderate resistance to pressure and cleaning chemicals. Clarity is typically good for this class of materials.
Thermoplastic Polyurethane (TPU)
Though suitable for fat and aqueous foods and dairy products, these formulations should not be used for foods with high alcohol. Thermoplastic polyurethane tubing products offer sealability and good clarity as well as some resistance to pressure, but may impart some undesirable taste/odor if not designed properly. Likewise, flexibility is determined by its material design.
Thermoplastic Elastomers (TPE)
This material can be used for aqueous foods and dairy products, but should not be used for foods with fat or high alcohol content. TPV offer high flexibility, sealability and a long pump life (1,000 hours); however, it has a low resistance to pressure and is opaque. The polymer also offers some resistance to cleaning chemicals but may have an adverse impact on taste/odor if not designed properly.
Styrenic Thermoplastic Elastomers
Though non-polar thermoplastic elastomers are suitable for aqueous foods and dairy products, this polymer should not be used for foods with fat or high alcohol content. These materials offer sealability, high flexibility and a long pump life (500-1,000 hours); however, it has low clarity and a low resistance to pressure. It also offers some resistance to cleaning chemicals.
Silicone Rubber
This polymer should not be used for products with fat or high alcohol content, but is suitable for aqueous foods and dairy products. Silicone rubber offers high flexibility and limited leachables, resulting in limited impact on taste/odor; however, it offers no sealability, limited resistance to pressure or cleaning chemicals and possesses poor optical clarity attributes. Given its flexibility, it can withstand moderate dynamic deformations associated with peristaltic pumping and offers 25-500 hours of pump life.
Fluoropolymers
These materials are suitable for products with fat and high alcohol content as well as aqueous foods and dairy products. Typically semi-rigid, fluoropolymers offer some limited flexibility and clarity, as well as high resistance to pressure and temperature, cleaning chemicals and leaching to offer a high resistance to any impact on taste/odor. They do not offer sealability.
Though dispensing tubing solutions can go a long way in meeting performance objectives, not all OEMs or brand owners have the expertise or resources necessary to determine the best tubing solution for a dispensing application.
Key is a tubing solutions supplier with comprehensive design capabilities and materials science know-how to help OEMs design high-performance dispensing equipment that protects the consumer and the brand’s integrity and achieves reduced downtime and long-term cost savings.
Looking for a reprint of this article?
From high-res PDFs to custom plaques, order your copy today!