How increased SKUs, smaller orders impact the evolution of AS/RS
Discover how today’s automated storage and retrieval systems have evolved to stack up to the industry’s ever-changing demands.
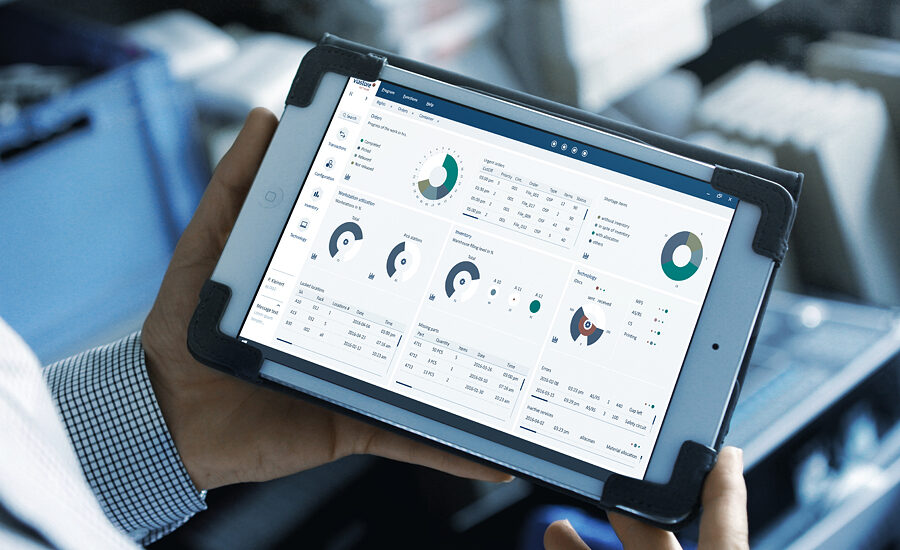
viadat 9.0 from Viastore boasts an intuitive, easy-to-configure and user-friendly interface that includes more than 2,500 functions for manual or automatic storage, picking and distribution.
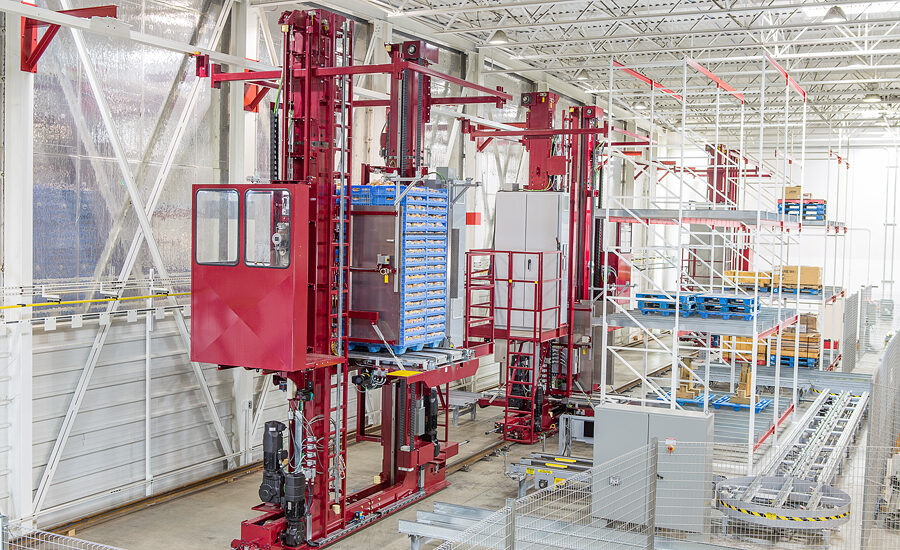
Westfalia introduced several upgrades to its storage and retrieval machines, including an independent service lift or moveable cab, built-in dual safety processors and higher payloads.
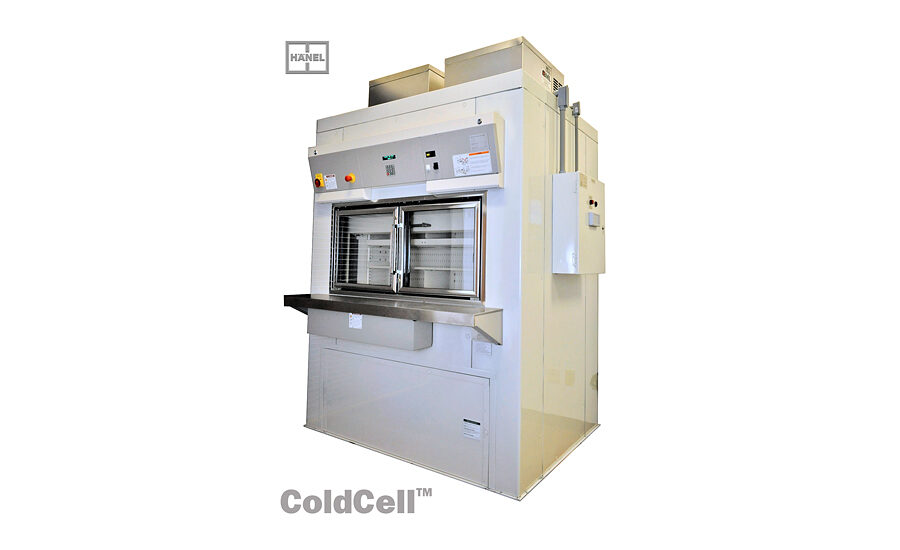
Hänel Storage Systems’ ColdCell is a comprehensive re-engineering of a Hänel carousel or lift to allow for refrigerated storage down to 5°F.



As the influx of e-commerce continues to rattle traditional brick-and-mortar stores, so too does the rise in stock-keeping units (SKUs), smaller quantity orders, just-in-time demands and the need for optimal storage volume, speed, flexibility and scalability.
Compound these issues with automation, traceability, labor shortages, increased regulations and plant and employee safety, and it’s no surprise many of today’s manufacturers are continuously transforming their automated storage and retrieval systems (AS/RS).
“Increased SKUs and smaller order quantities are a persistent and continuing challenge for the food and beverage distribution market,” says Victor Hoerst, sales account manager of Murata Machinery USA, Inc., Charlotte, N.C. “Of course, food and beverage manufacturers still have their flagship/fast running products, but their customers continually demand greater variety. This proliferates the number of SKUs that a manufacturer must make. AS/RS technology can be a great strategy to productively, efficiently and accurately manage this complexity.”
The global AS/RS market is forecast to be worth $8.43 billion by 2022, according to the “Automated Storage and Retrieval System (ASRS) Market by Type (Unit Load, Mini Load, VLM, Carousel, Autostore, & Midload), Function (Assembly, Storage, Order picking, Kitting, & Distribution), Industry, and Geography - Global forecast to 2022.”
The report, published by MarketsandMarkets, Seattle, Wash., reveals Europe to hold the largest share of the global AS/RS market, with factors such as high degree of accuracy, improved efficiency, high-throughput inventory management capabilities and increasing demand for technologically advanced systems depicted as key drivers of growth.
Flexible design
In response to growing global demand in both North America and Europe, Westfalia Technologies, Inc., York, Pa., introduced several upgrades to its storage and retrieval machines (S/RMs). For example, the independent service lift or moveable cab provides operators and maintenance technicians a safer alternative to travel to various levels of the system that is independent of the vertical lift station (VLS). Built-in dual safety processors and a greater range of sensor communication between the S/RM, operators and maintenance staff are said to meet the highest European and U.S. safety standards. Standard payload for an S/RM is now 6,000 pounds, with optional higher payloads available. And, systems can now operate at temperatures as cold as -40°F, perfect for frozen food warehouses.
“The majority of refrigerated and frozen food warehouses employ manual operations, requiring staff to pick and pack orders in frigid conditions. However, some companies are recognizing that these conditions are not only hazardous for employees, but also unfavorable for warehouse operations as a whole,” says Dave Williams, director of software and solutions delivery for Westfalia. “Forward-thinking food and beverage companies are looking to automation to promote safer work conditions for employees and gain new warehouse efficiencies. Automated technologies, such as a high-density AS/RS, can pick products in refrigerated and frozen warehouses without the need for breaks and with greater accuracy and speed than humanly possible. Further, an AS/RS allows companies to better utilize their existing space by storing more product within the same (and often smaller) building footprint.”
Westfalia also completed a multi-million dollar test facility at its York facility to test improvements and new software user interfaces. It will also serve as a training facility with hands-on, improved training on AS/RS.
Reliable refrigeration
For users who require a portion of their inventory to be stored in a refrigerated or frozen state as opposed to their entire inventory, Hänel Storage Systems, Pittsburgh, Pa., offers ColdCell, a comprehensive re-engineering of a Hänel carousel or lift to allow for refrigerated storage down to 5°F. The interior is redesigned to allow for additional air circulation, while the exterior is encased within a heavily insulated cell that maintains the full storage capacity. Plus, the refrigeration hardware and controls are custom-designed to include digital displays with access control, programmable thermostats and redundant backup systems to ensure uninterrupted operation when storing sensitive inventory.
“One of the trends driving today’s market is the need for customized solutions that allow integration with a myriad of software systems. Inventory management programs are intelligent systems for computerized handling of warehouse processes,” says David Phillips, marketing manager for Hänel Storage Systems. “Automated equipment runs faster and more efficiently than manually operated equipment. In the case of AS/RS equipment, staff can pick and place more product in less time with fewer people for significant time savings.”
User-friendly features
Viastore, Grand Rapids, Mich., updated the warehouse management software (WMS) behind its AS/RS. viadat 9.0 boasts an intuitive, easy-to-configure and user-friendly interface that includes more than 2,500 functions for manual or automatic storage, picking and distribution. This means that the WMS can be used across multiple locations and international borders, and allows for uniform, streamlined intralogistics processes throughout the company.
Viastore also introduced viaflex3, a case handling shuttle system that provides more flexibility over viaflex2 by accommodating out-of-the-AS/RS-aisle movement. viaflex³ makes optimal use of each square and cubic meter. Aisle- and level-independent, these shuttle vehicles transport goods without complex conveyor systems.
“The trends driving food and beverage are predominantly focused on how to handle SKU proliferation and improve accuracy,” says Brad Moore, vice president of sales for Viastore. “The requirements for food handling and safely managing allergen products have put a strain on all conventional warehousing solutions where there is a great dependency on the human. These allergens (peanut, gluten, lactose, egg, etc.) are creating additional SKUs of raw materials, but also a significant increase in SKUs with the finished products.”
Automated inventory staging
Dematic, Grand Rapids, Mich., introduced Multishuttle 2, an automated inventory staging buffer system designed to accommodate totes, trays and cases weighing up to 110 pounds, says Tom Steininger, market development manager.
Fifty percent lighter and twice as fast as its predecessor, the Dematic Multishuttle 2 incorporates advanced engineering and aluminum construction to create a lighterweight device, faster operating speeds, higher payload capacity and multi-deep storage capability.
“AS/RS technologies have been around since the late 60s, and have continuously evolved to improve their capabilities to function reliably in ambient to extreme temperatures,” says Michael Clemens, principal consulting engineer for Bastian Solutions, Inc., Indianapolis, Ind. “As the IoT drives a need for small order quantities and fast order turnaround times, the continued improvements in shuttle technologies for both unit loads and individual cases have been turned into highly efficient goods-to-person fulfillment systems.”
WHAT THE FOOD INDUSTRY CAN LEARN FROM PHARMA
When it comes to comparing food vs pharmaceuticals, there’s more similarities than differences. For example, both are heavily regulated industries that rely on traceability, product safety and SKU management to succeed. Both also depend on automated storage and retrieval systems (AS/RS) to fulfill orders, minimize spacing issues and meet customer demands.
More importantly, the same temperature-controlled environment technologies used in the pharmaceutical industry can be applied to the food and beverage industry, says David Phillps, marketing manager for Hänel Storage Systems, Pittsburgh, Pa.
“Just as AS/RS equipment in pharmaceutical cleanrooms maintain constant low temperatures and protect against contamination, the same can be done for certain foods,” he adds.
Meanwhile, the speed and reliability of an AS/RS allows pharmaceutical and food and beverage manufacturers to employ just-in-time order fulfillment strategies, says Michael Clemens, principal consulting engineer for Bastian Solutions, Inc., Indianapolis, Ind.
“Add the absolute requirement for accuracy in pharmaceutical distribution to food and beverage, and you can see where the reliance on AS/RS systems with absolute efficiency and accuracy are critical,” says John Ashodian, marketing manager, logistics automation for SICK, Minneapolis. “A system that integrates the capabilities intelligent sensing devices offer will be able to provide the transparency needed to confidently meet consumption and service demands.”
Looking for a reprint of this article?
From high-res PDFs to custom plaques, order your copy today!