Not your average cold food packaging label
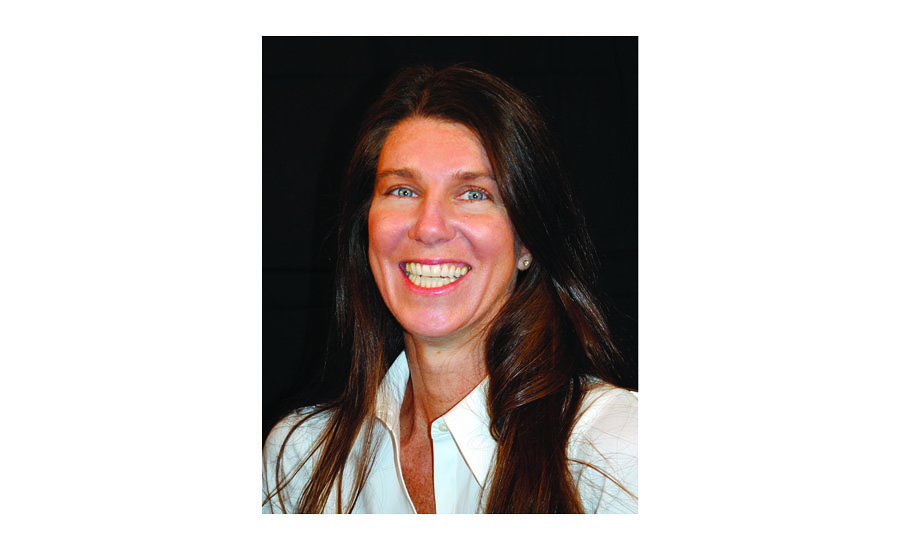
In today’s cold food industry, refrigerated and frozen foods manufacturers are faced with an increasing number of challenges – from making sure products are easy to ship and transport to meeting necessary compliance regulations. And, while product packaging and labeling might not seem important in the overall equation, these two finishing components are vital to ensuring products make it through the cold food chain successfully.
A cold food package, for example, is precisely designed to keep cold food and beverage products fresh, preserved and protected. But, in order to do so, there are many factors manufacturers need to consider, such as storage, shelf life, varying environments and temperatures, the possibility of food package interactions, costs and branding. And, although cold food labeling comprises just one small piece of the entire packaging process, should the label fail, the resulting implications can be enormous.
For example, a statistic in a June 2016 consumer insights study by WestRock Co., Norcross, Ga., says roughly 65% of consumers have admitted to trying something new because the package caught their eye. Likewise, according to Business Insider, first impressions take about seven seconds, making subsequent judgments based on quick information. Given facts like these, consider how cold food sales would fare if packages featured labels that were falling off or had fallen off? Refrigerated and cold food labels may be primarily intended to communicate important product messaging, nutrition information and branding information, but they also help products sell.
Therefore, cold food manufacturers need product packaging labels that are visually appealing, showcase superior product packaging, adhere quickly and easily, conform to a variety of packaging types and stay in place as intended for the product’s life cycle. And, one of the biggest challenges in accomplishing this is ensuring labels will withstand the extreme cold, wet, freezing or changing application conditions of cold food packaging.
For example, frozen foods labels can become stiff and fall off in the freezer. If outdoor temperatures are hot and humid, refrigerated foods labels may flag or fall off when transported from store to home. Similarly, in beverage labels, bottles often move from place to place, like a cold refrigerator to a warm car, creating condensation and affecting label performance. In any case, the last thing a brand owner wants is for a label to degrade or peel off a package.
New advances in cold food adhesive labels
Traditionally, cold food labels have included either solvent- or emulsion-based adhesives. However, due to recent efforts to reduce VOC (volatile organic compound) emissions and improve air quality, solvent-based adhesives are being used less and less. This is paving the way for an economical, more environmentally friendly adhesive option known as hot melt.
In addition to environmental benefits, emulsion-based adhesives are known for advantages such as ease of use, safety and strength.
Hot melts are cool
Hot melt adhesives are made without solvents or water, resulting in an even more efficient production process than that used with emulsion-based adhesives. Without water, hot melt adhesives dry extremely fast, producing better quick tack and creating a strong bond between merged surfaces. This is especially beneficial for difficult-to-adhere-to low surface energy substrates commonly found in the food packaging industry, like low-density polyethylene (LDPE) and high-density polyethylene (HDPE). Hot melt adhesives are also designed for use on cardboard, plastic films, polypropylene and polyester.
Additionally, one of the greatest benefits of hot melt adhesives is that they are said to deliver unmatched versatility for any temperature application – warm or cold. Some cold food labeling hot melt adhesives are specially formulated to stay adhered from temperatures as cold as -65°F to temperatures as warm as 150°F. And, they can be applied at temperatures as low as -10°F. With these adhesives, neither sub-zero temperatures nor heat is an issue.
Other advantages of hot melt adhesives include:
- Hot melts are known for their “high tack,” or ability to grab quickly to a surface.
- Hot melts form a strong initial bond when applied, successfully sticking to difficult-to-adhere-to surfaces like low-surface energy materials.
- Hot melts ensure secure, lasting adhesion, keeping labels in place.
- Hot melts maintain water-resistance properties, allowing labels to maintain adhesive integrity and aesthetic appeal if exposed to water or moisture.
- Hot melts are low-VOC and contain no solvents, delivering a more environmentally friendly adhesive option.
From frozen foods to meat and poultry
Some of the most common cold food labeling applications using hot melt adhesives today are general refrigerated and frozen foods, beverages, meat and poultry, cheese and corrugate. Hot melt adhesives are performing well in these label applications because they can meet needed durability despite cold, moisture and repeated product handling.
For instance, high-priced meat and poultry items often require packaging, labeling and shipping in cold storage as well as repeated product handling. In cheese packaging, shrink film is a commonly used packaging material, but can harden in cold temperatures. When cheese is packed, transported and stored, temperatures typically range from 34-38°F.
No matter the cold food labeling application, hot melt adhesive labels are gaining in popularity and performance – quickly becoming the refrigerated and frozen foods packaging label of choice.
Looking for a reprint of this article?
From high-res PDFs to custom plaques, order your copy today!