Techniques for improving your company’s supply chain
The most important step to success is to gain visibility to the components that are contributing to your performance.
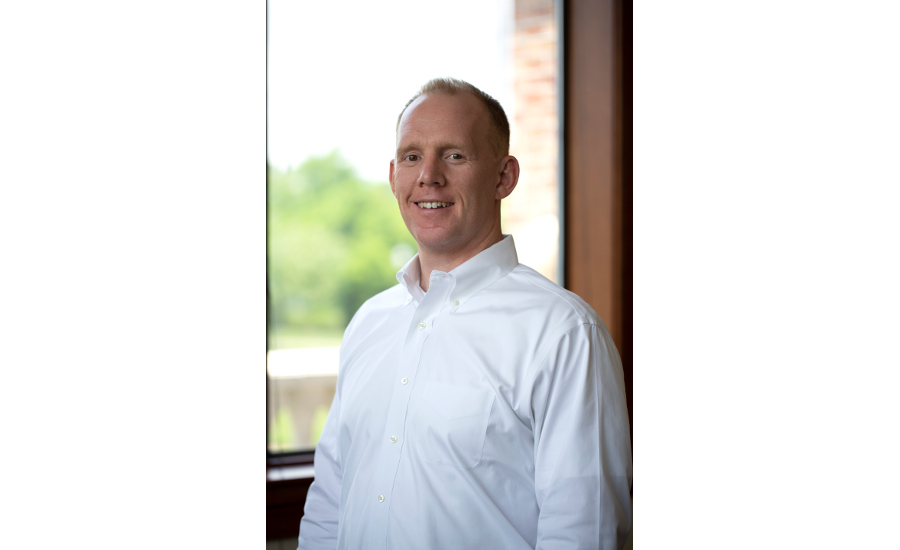
Supply chain improvements can be a substantial undertaking for companies of any size, and often require years to complete. However, it is a task that can deliver substantial benefits in terms of improving efficiencies, enhancing customer service and minimizing a company’s environmental footprint. Here’s how companies can improve their product’s path to market:
Reducing complexity. The most efficient way to improve the supply chain is to reduce the complexity of the transactions required to move an item from end to end. We are all better basketball players if the rim is 3 feet off the ground. Some common complexity reducing projects are inventory bearing location (IBL) consolidation, software integration, transportation routing optimization, production location rationalization and SKU rationalization.
There are numerous strategies that can be utilized to reduce the complexity of a supply chain, including supply chain design software applications available from vendors experienced in complexity reducing efforts.
These applications gather structural and policy parameters to create a digital “twin” of the supply chain that simulates a system operating at optimal efficiency. Hypothetical changes reveal new ways to operate under “what-if” scenarios to reveal possible real-world changes that can lead to enhanced efficiency.
While the resulting optimal supply chain isn’t always entirely realistic to implement, it creates an end-state target for an organization to methodically and opportunistically move toward.
Enhancing visibility. Each organization maintains key metrics to measure the efficiency and performance of its supply chain. We have all pursued initiatives to increase inventory turns, improve on-time deliveries and fill rates or reduce costs. The most important step to success in these efforts is to gain visibility to the components that are contributing to your performance. It is paramount to gain visibility of the root cause of your performance issue to create an appropriate corrective measure. Visibility can be as simple as excel spreadsheet trackers, but their impact is immense. This information can be used to create a targeted corrective action plan that can be shared with internal and external stakeholders.
Assigning accountability (who’s on first?). Despite your efforts to reduce complexity, your organization will still be required to create a process. This process will inevitably require multiple employees to follow a playbook to move an item through the supply chain from end to end. Because employees bear some responsibility for this action to occur successfully, it is necessary for all involved to clearly understand their role. Process mapping exercises can be as complex as a full value stream mapping (VSM) project or simple standard operating procedures. This process requires employees from different departments to understand the implications of their actions on other departments. The point at which a process passes from one department to another is typically where most failures occur. The root cause for the errors and the possible solutions are usually identified by bringing departments together and mapping out all transactions. Creating solutions with multiple departments will improve performance and foster an environment of teamwork.
The end result of all these methodologies can eliminate redundancies, reduce complexities, lower operating costs, decrease carbon footprint and improve customer service. Those are goals that a company of any size can embrace.
Looking for a reprint of this article?
From high-res PDFs to custom plaques, order your copy today!