ProFood Tech 2019: Comprehensive solutions for food, beverage professionals
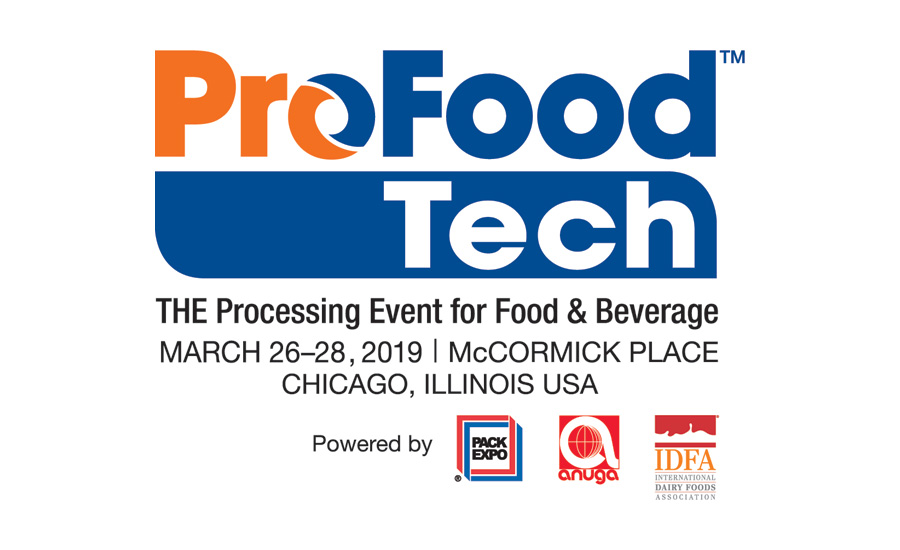
ProFood Tech 2019 returned March 26-28 at Chicago’s McCormick Place, hosting more than 7,000 visitors and 450 exhibitors in excess of 150,000 square feet.
Powered by PMMI, the Reston, Va.-based organization that produces the annual PACK EXPO shows; Koelnmesse, the Germany-based producer of Anuga FoodTec; and the International Dairy Foods Association (IDFA), Washington, D.C., this biennial show addressed key issues impacting the food and beverage processing industry.
Here is a rundown of some of the latest innovations introduced and showcased at ProFood Tech 2019.
HEAT EXCHANGERS, POSITIVE-DISPLACEMENT PUMPS

HRS Heat Exchangers, Marietta, Ga., showcased a number of solutions, including its AF Series and the new Asepticblock Mini Series aseptic fillers.
The HRS Product Recovery System measures a physical or chemical property (such as product Brix, pH, viscosity or density) and automatically alters the treatment of it. This reduces the amount of wasted product at production changeovers or when implementing cleaning-in-place programs.
The HRS BP Series of reciprocating positive-displacement pumps feature a hygienic design that incorporates a separator between the piston and the hydraulic chamber to ensure there is no contact between the product chamber and the hydraulic oil. Once the pump is in operation, no part that comes into contact with oil can come into contact with the product. The pumps are capable of flow rates between 52.8-5,280 gallons per hour with a pressure drop of up to 435 psi.
HRS Heat Exchangers
770-726-3540
www.hrs-heatexchangers.com
HIGH-END PACKAGING SOLUTIONS

SÜDPACK Packaging Group, Germany, exhibited its portfolio of packaging solutions for the dairy, meat, poultry and seafood market. Following the acquisition of Seville Flexpack in late 2017, SÜDPACK is expanding its North American business by introducing new high-end packaging solutions and increasing production capacities at its Oak Creek, Wis., site.
For instance, SÜDPACK showcased Veraplex, a thin film that offers technical features such as puncture resistance, excellent barrier properties and tear resistance.
In turn, the Multipeel xPET ensures safe sealing on all kinds of trays and hard PET films at a low sealing temperature of 293°F. Multipeel High boasts high resistance to tearing, making disruptions during the packaging process a thing of the past. Multipeel Flow Wrap is a resealable bag that can be opened and securely sealed intermittently with no clip or zipper. The special appearance of the packaging makes it stand out on the shelf compared to bags offered by the competition.
SÜDPACK’s Multiclose packaging concept for thermoformed resealable packs make it possible to produce practical, resealable packs using standard thermoforming systems and offers simple opening and resealing.
SÜDPACK Packaging Group
414-761-2751
www.suedpack.com
SANITARY PUMPS

NETZSCH Pumps North America, Exton, Pa., showcased sanitary pumps ideal for a wide range of food applications.
For instance, the NEMO BH Sanitary advanced pump is appropriate for clean-in-place processes when provided with optional flushing connections. It also meets 3A standard requirements, and can be disassembled quickly for easy cleaning. The exclusive NEMO progressing cavity modular pump design, combined with food-grade Nitrile, EPDM or Viton stators, makes it ideal for flows up to 200 gallons per minute, pressures of 360 pounds per square inch and particle sizes up to 2.5 inches.
The NEMO BO sanitary prime open hopper pump is an FDA-compliant pump for non-free-flowing applications, specially designed to handle high-consistency products with a low degree of flowability. These pumps provide continuous pressure-stable, gentle and low-pulsation conveyance with metering in proportion to rotational speed. The pump handles flows up to 880 gallons per minute, pressures up to 360 psi and particle sizes up to 3 inches.
NETZSCH Pumps North America
610-363-8010
https://pumps.netzsch.com
CHECKWEIGHING & METAL DETECTION IN ONE INTEGRATED SYSTEM

The CM33 CombiChecker product inspection system from Mettler Toledo, Lutz, Fla., integrates two key inspection functions into one simple solution. Within a single compact system, products pass through a metal detector, are then weighed on a checkweigher. Products detected to be contaminated with metal, or that are beyond weight parameters, are immediately rejected from the production line into separate reject bins for each defect. Users can select from a number of conveyors, guide rails, transfer plates, dual locking reject bins and rejector types to customize their solution. These mechanical features are then complemented with choices from a complete library of line integration, functional and operational, production monitoring and control and communication options.
The X34 X-ray inspection system provides detection of metal, glass, high-density plastic, mineral stone and calcified bone fragments across a wide range of packaged foods. The X34 is a single lane x-ray system designed for the inspection of a wide range of small and medium-sized packaged products. One of its key features is a 100W “Optimum Power” generator, which automatically maximizes detection sensitivity. This is complemented by an advanced 0.4-mm detector for the accurate detection of very small contaminants. The high-performance software also allows for automated product setup without the need for manual adjustment from the operator. In addition, the X34 can be equipped with the ProdX advanced data management tool, which maximizes production efficiency and quality control. The ProdX software can store images of foreign body contamination, which can be viewed remotely, in full support of connectivity, traceability and compliance. The system also features a highly-responsive capacitive touchscreen, allowing users to increase the viewing angle of stored images while maintaining image consistency.
METTLER TOLEDO Product Inspection
813-889-9500
www.mt.com
AUTOMATED PACKAGING TECHNOLOGY

Schubert North America, Charlotte, N.C., introduced the new Flowmodul system, which is said to save up to 70% of floor space compared to a mechanical flow-wrapping machine.
With this unit, the flow-wrapping process is entirely integrated into a TLM picker line. This enables a slim and compact machine layout. At the same time, the machine’s high efficiency of over 99% ensures better performance, and the flow-wrapping component enables effective quality control of the products to be packaged and flexibly adapted to a wide variety of requirements, including small batch sizes, frequent product changes and a large variety of highly sensitive products.
The pick-and-place robots carefully place any conceivable product into the flow-wrapping component’s feed system. Moreover, upstream image processing with a 3D scanner performs the optical quality control of the products to be packaged. It checks position, orientation, shape, color and volume as per the customer’s specifications. This ensures that only faultless goods are picked up by the F4 robots and placed into the feed chain.
The Flowmodul also offers maximum flexibility in terms of product mix. And, thanks to a new sealing technology developed by Schubert, the highly efficient flow-wrapping component also packs heat-sensitive products.
Schubert also expanded its Charlotte North American headquarters to include a new manufacturer’s training center, where two training machines provide hands-on operator training.
Schubert North America
980-244-3140
www.schubert-na.com
REUSABLE, RETAIL-READY MERCHANDISING SYSTEM FOR RETAIL DELIVERIES

ORBIS Corp., Oconomowoc, Wis., launched a fully reusable, retail-ready, one-touch merchandising system designed for retail deliveries.
The XpressBulk Milk Delivery System transports fluid milk from the truck to the retail cooler with only one touch.
Comprised of a dolly, removable handle and four plastic contoured trays, the XpressBulk Milk Delivery System allows for easy transport off the truck and right into the cooler for quicker unload. Once the system is placed in the cooler, consumers can shop directly from the XpressBulk Milk Delivery System without any unpacking or additional touches needed. Plus, the dolly and trays are custom designed to fit the bottle being transported.
The small-format footprint and contoured optional handle of the new system allows it to be easily maneuvered through narrow aisles and doorways. When it’s not being moved, the handle can be removed for increased storage room in and out of the coolers. Also, the dolly’s condensed height allows the ability to cube out merchandising coolers, creating space for additional SKUs and ultimately increasing sales.
Even after use, the XpressBulk Milk Delivery System provides storage and return efficiencies. Its trays collapse into one another for a snug fit, and the dollies can be stored on top of each other for optimal space in backrooms. In addition, color-coded trays visually cue employees to stack them for efficient nesting for return trips. The XpressBulk Milk Delivery System is also designed to interface with standard material handling equipment. Together, these features support the entire retail supply chain, from the manufacturing plant to the retail aisle.
ORBIS Corp.
800-890-7292
www.orbiscorporation.com
MOTION CONVEYOR SYSTEMS

Precision Food Innovations (PFI), a Pella, Iowa-based company developed by KOFAB, Algona, Iowa, and Meyer Industries, San Antonio, Texas, exhibited its latest material handling technology, including the PURmotion horizontal motion conveyor, Eleveyor, Curveyor and Vibratory Bowl Feeder.
Precision Food Innovations
515-295-7265
www.pfi-global.com
Looking for a reprint of this article?
From high-res PDFs to custom plaques, order your copy today!