Employee Health & Safety in Cold Food Facilities
OSHA says employers have a responsibility to provide workplaces "free of recognized hazards, including cold stress.”

While OSHA does not have a specific standard for employees working in cold facilities, the federal agency says employers have a responsibility to provide workers with a safe environment. Courtesy Getty Images
From on-the-job training to on-the-job healthcare, cold chain employers are looking for ways to attract and retain a happy and healthy workforce.
Cold and frozen food companies know there’s a limit to how long workers can be in frigid areas. While the U.S. Occupational Health and Safety Administration (OSHA) does not have a specific standard for employees working in cold environments, the federal agency says employers have a responsibility to provide workers with a workplace "free of recognized hazards, including cold stress” and should train employees “on preventing and recognizing cold stress illnesses and injuries.”
The fear of making mistakes can lead to hesitation, reduced productivity and even accidents. In food production, safety incidents lead to direct costs such as medical expenses and indirect costs like lost productivity, increased insurance premiums and potential legal fees, not to mention potential food safety implications.
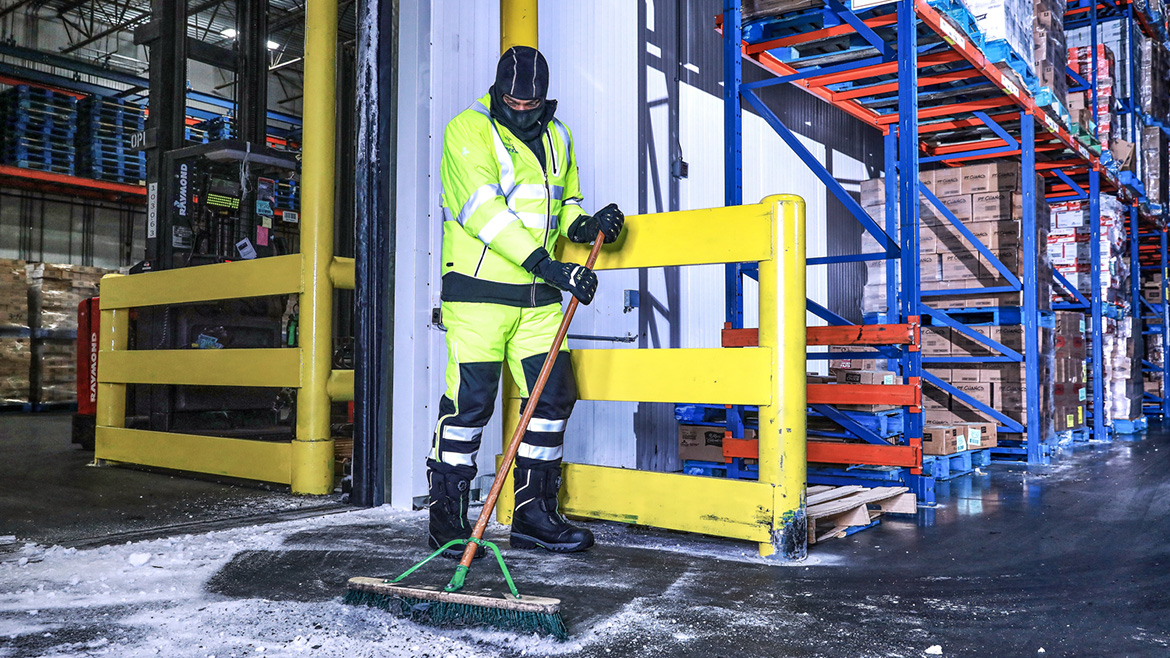
A report by the National Safety Council lists the average cost of a workplace injury at $40,000, with a total estimated economic impact of $167 billion in 2022 alone.
WorkForge designs health and safety and food safety training modules that break down essential information into easily digestible segments that can be completed at their own pace, fitting into their schedules without disrupting production.
"When training is tailored to specific tasks and hazards, it becomes more relevant and engaging for employees, leading to better retention and application of safety practices. Frequent, bite-sized training sessions ensure that safety practices remain top of mind, reinforcing knowledge and skills over time,” said CEO Nate Walts. “This continuous reinforcement is essential for maintaining a culture of safety, as it helps employees stay updated on the latest protocols and reduces the likelihood of accidents. By incorporating regular, focused micro-modules into your safety training program, you can significantly enhance the effectiveness of your training efforts, ensuring that your workforce is always prepared to operate safely and efficiently.”
Specific to the cold chain, the company offers trainings on food safety, temperature control and monitoring, regulatory compliance and general workplace safety.
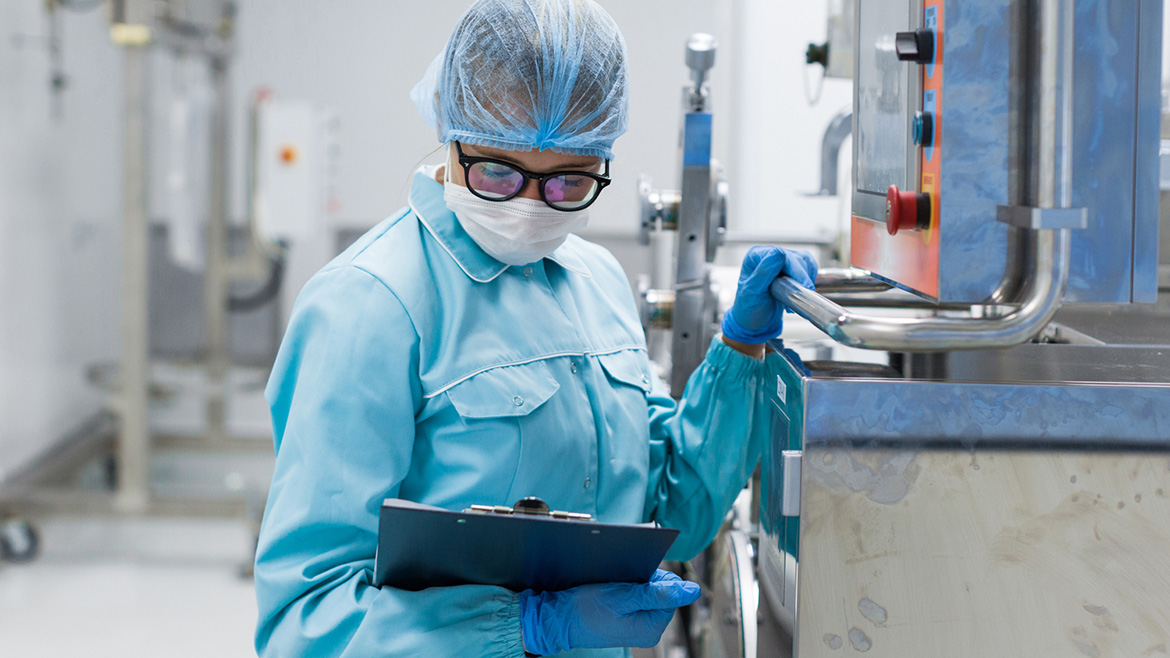
"Many organizations believe that employee training is costly, time-consuming and only necessary for new hires. In reality, offering ongoing, tailored training programs are critical for reducing errors, improving productivity and ensuring compliance. These programs lead to long-term cost savings, higher employee retention, better product quality, and ultimately, a positive impact on the bottom line, making them a valuable investment for any organization,” Walts said. “WorkForge also offers robust maintenance training pathways that are essential for cold food processors, manufacturers and storage providers. At the heart of this offering is our Maintenance Content Library, featuring the Maintenance Tech Fundamentals pathway—a foundational series designed to bring every general maintenance technician up to speed with essential preventive maintenance tasks. For those looking to specialize further, our Functional Pathways provide in-depth training, whether it's for a general maintenance technician or a senior technician mastering all disciplines. This comprehensive training ensures that your maintenance staff and operators can keep equipment functioning smoothly, prevent costly breakdowns, reduce downtime, and ultimately contribute to a more reliable operation and a healthier bottom line.”
A 2023 Swedish study found that workers in cold storage environments were at higher risk of neck, shoulder and lower back pain than those working in moderate temperatures.
When designing a new, 100,000-square-foot facility for United States Cold Storage in Lake City, Florida, design-build firm Stellar worked with automation company Westfalia, and material handling company, Crown, to design a conveyor system for forklift-like turret trucks to move through very narrow aisles (VNAs) of only 75 inches to store and retrieve products.
“The turret trucks allow fewer people to complete the storage and retrieval process, so employees can rotate through, reducing their cold exposure. Plus, there’s less need for workers to handle heavy items themselves, which lowers their back and neck pain risk,” said Gregory Baker, project manager at Stellar. “In addition, the facility has safety sensors that prevent employees from opening doors into the trucks’ path. The ability to work more efficiently is another important factor in reducing workers’ time in cold temperatures.”
Employees should wear cold-weather-approved gear, including jackets and hats. Hands should be protected, not just from cold but from equipment vibrations that can cause injury. Clothing should be layered and loose-fitting and should not absorb sweat or water. Footwear should be insulated and slip-proof and garments should include feature like accordion-stretch panels at the knees, elbows, waist and shoulders that allow for a greater range of motion without riding up or bunching, which creates an uncomfortable distraction and increases the body’s exposure to the cold.
“Working in consistently cold temperatures, often subzero temperatures, requires both mental and physical toughness. People just starting out in the business often have a misconception that their regular winter coat will be sufficient to help them do the job. They underestimate how exposure to relentless cold will make their bodies feel clumsy and dull their reaction times,” said Leigh Stadelmeier, vice president of B2B outdoor sales at RefrigiWear and an authorized OSHA outreach trainer. “More of our customers in the cold storage industry are moving to high-visibility workwear that meets ANSI/ISEA standards for bright materials and reflective tape that are more easily seen in a dimly-lit warehouse.
For businesses that want to make the switch to high-visibility insulated PPE, we offer training sessions on the different levels of ANSI/ISEA standards and meet customers and their employees to field test insulated garments, gloves and boots in specific environments in which they’ll be used,” he said. “What’s unique about this industry is that temperatures and conditions are meticulously controlled. Unlike folks working outside in unpredictable winter weather, people working in these controlled indoor environments know exactly how cold it will be, the wind chill they’ll face from operating a forklift or being near air circulators, and how long they’ll be exposed to the cold before a warming break. So, they have the advantage of selecting insulated workwear to suit conditions in the facility and the activity level required in their job. It takes the guesswork out of getting the right level of protection from frostbite, hypothermia and other cold stress injuries.”
Once hired, companies are looking for ways to keep their employees healthy and happy, deterring turnover. Ruiz Foods, makers of the No. 1 selling Mexican frozen food in the U.S., has opened health centers at three plants over the last year – in Dinuba, California, Florence, South Carolina, and Denison, Teas.
Operated by CareATC, the centers provide insured team members and their covered family members, access to services like primary care, allergy treatment, sports physicals, labs/vaccinations, chronic condition management, generic medications and annual physicals without any co-pays or additional costs.
“Across the country and in the communities where we do business, we see and hear about the need for higher quality healthcare, that is easier to access, at a lower cost. There are nearly 7,000 on-site health/wellness centers in the United States; only 15% of organizations the size of Ruiz Foods provides the benefit of an on-site health center, but it was a key desire for our team members. Making healthcare easier to access and more affordable will help us continue our quest to remain one of the best places to work,” said Tony Caetano, SVP of Administration at Ruiz Foods.
The company expects it will take three years for the clinics to scale to a full patient load.
“While we don’t have a lot of hard data on recruitment and retention yet, we know that our team members and community have been excited about our health centers and see it as a great benefit. It’s important for us to make it as easy as possible for our team members to seek the healthcare they need. Anecdotally, we have been heartened to hear from team members who went in for preventative care and have identified potentially serious conditions that they were able to address because they had the opportunity to seek that preventative care,” Caetano said. “The convenience of an on-site health center is proven to improve Team Member health while lowering the cost of care for them and the company. However, while there can be long-term financial benefits by having a healthier workforce, we did not add health centers for cost-savings and wouldn’t recommend anyone else do it solely for that reason. It needs to be about the benefit to employees and the prospect of a healthier workforce.”
Looking for a reprint of this article?
From high-res PDFs to custom plaques, order your copy today!