Food Logistics Forum Zeroes in on Automation, Sustainability and Energy Management
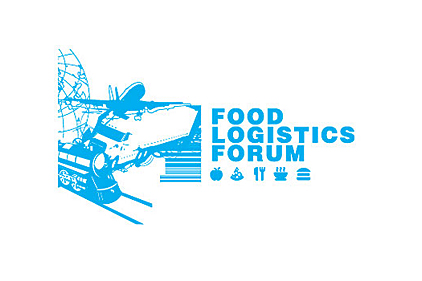
With the outside temperatures topping off at 105°F, it can’t be that challenging to think about refrigerated and frozen foods. Nothing like a hot heat to talk about cold foods, right?
Nonetheless, several refrigerated and frozen food processors, suppliers and cold storage and warehouse providers beat the heat for this year’s Food Logistics Forum, which took place June 2-4 at the Westin Lake Las Vegas in Henderson, Nev.
Co-hosted by the American Frozen Foods Institute (AFFI), McLean, Va., and the Global Cold Chain Alliance (GCCA), Alexandria, Va., the Food Logistics Forum provided participants with the educational resources, regulatory information and business development opportunities needed to navigate the ever-changing logistics landscape.
Refrigerated & Frozen Foods’ editor-in-chief Marina Mayer ventured out west to cover the event and to present Hormel Foods with the 2013 Sustainable Supply Chain of the Year award. If you couldn’t make it to this one-stop-shop for supply chain and logistics solutions, here’s a snapshot of what you missed:
The conference kicked off with an opening session presented by Greg Gilmer, logistics coordinator at NORPAC Foods, and Marty Steinmetz, president of national accounts for U.S. Cold Storage, followed by a series of sessions.
Retail 2020: What the Future Will Bring.
Troy Beeler, client development manager for RetailNet Group, Waltham, Mass., discussed what the future brings to the food retail industry and how to better analyze the different retail categories.
“If you take the roof off of your typical supercenter and break it apart category by category, then you can tell where the retailers’ strategic planning lies,” he notes.
Some take-away points RE: retailers’ challenges:
- Provide something different for three generations.
- Develop products for globalizing food palettes.
- Meta-apps are on the rise and will enhance a customer’s in-store experience.
- Every retailer needs a food-to-go program.
- Growth is in discount and fresh.
- The future of convenience—rolling up quick-service restaurants into independent retailers with a coffee trip.
State of the Trucking Industry.
Bob Costello, chief economist for the American Trucking Association, Arlington, Va., provided facts and figures pertaining to the state of today’s—and tomorrow’s—trucking industry. For instance, truck-load intermodal increased 7.6%, truck loads 3.5% and revenues per mile 4.7%, since last year. However, total miles dropped 2%, while the average length per haul declined 4.8% since last year, as a result of rail intermodal. Yet, the challenge of keeping drivers remains the challenge.
“Companies need to have programs in place that keep drivers, and keep quality drivers,” Costello recommends. “If the economy improved twofold, there simply wouldn’t be enough trucks on the road to keep up with supply [due to driver turnover].”
In his presentation, Costello also provided facts pertaining to the construction and real estate industries, as well as driver turnover.
Maximizing Rail Car Fleet through Collaboration.
Belinda Hess, director of marketing and food consumer for CSX Transportation, Jacksonville, Fla.; Dwight Price, director of sales and marketing for Cryo-Trans, Owings Mills, Md.; and Mark Sampson, director of logistics for ConAgra Foods Lamb Weston, Omaha, Neb., talked about how to maximize rail car fleet through collaboration.
For example, rail delivers significant scale efficiencies at higher levels, Hess says. In fact, railroads have re-invested $55 billion since 2008.
Over the next 15 years, 54% of U.S. temperature-controlled rail fleet will disappear, Price says.
And Sampson revealed the top challenges of stakeholders—shipper internal organization, warehouse efficiency, rail service design and car leasing strategy.
Creating Innovative Ways to Meet New Global Demands.
Andrew Cafcalas, senior manager of forward warehouse network for Sysco Corp., Houston, Texas, offered up innovative ways for manufacturers to meet consumers’ ever-changing demands, whether it be an online ordering app or an inventory app.
“We’re only as good as our last order,” he says.
Is Refrigerated Intermodal for You?
This roundtable—consisting of Katie Baker, director of temperature-controlled intermodal for BNSF Railway Corp., Fort Worth, Texas; Arthur Adams, director of sales for CSX Domestic Intermodal, Jacksonville, Fla.; Coby Bullard, president of intermodal for C.R. England, Salt Lake City, Utah; and Pat Boss, director of public affairs for Cold Train Intermodal, Overland Park, Kans.—brought to the forefront the real facts and issues concerning refrigerated intermodal and why this may be the most environmentally-safe solution for cold food producers.
For instance, “rail is the most environmentally-preferred mode of transportation,” Baker says.
“Nearly 14% of truck freight is sub-optimized based on modal selection,” Adams adds.
And, “intermodal service reduces CO2 emissions by 52%,” Bullard says.
Cold Storage Energy Management.
Here, Marcus Wilcox, chief executive officer of Cascade Energy, Portland, Ore., and Richard Druce, senior project manager for SUPERVALU, Eden Prairie, Minn., provided a case study outlining best practices for building and executing an energy program.
“Before energy programs were in place, energy was the second highest expense behind maintenance and employee wages,” Wilcox says. “Energy management is tactical, not strategic.”
Druce shared some insight into SUPERVALU’s energy savings after putting an energy management program in place. “Refrigeration, warehouse/lighting, battery chargers and doors account for about 70-80% of a site’s energy use,” says Druce. “Executive support is mandatory for a successful energy management program.”
An Update from Washington.
Kraig Naasz, president and CEO of AFFI, provided an update to the comings and goings of Washington with respects to the Food Safety Modernization Act (FSMA), food taxes and nutrition standards for school meals.
Naasz also talked about Frozen Food Roundtable, the initiative to change the way consumers think and feel about frozen foods.
“Consumers don’t understand how products are made, so we want to bring them back to the frozen foods aisle,” he adds.
Naasz also discussed Frozen FoodPac, which exists to advance the public policy advocacy efforts of the frozen food industry.
Processor Best Practices.
Chad Claude, director of logistics planning for Schwan Food Co., Marshall, Minn., discussed a variety of best practices, including:
- Logistics initiatives (unit load optimization, material handling practices, slip sheet vs. pallet strategies, temperature abuse and cold chain assessment).
- Temperature-controlled improvement initiatives (utilizing telematics to track and trace).
- Standard operating procedures (for example, trucks that are left running longer than usual).
- Improving traceability from raw materials to the consumer.
- Improving food safety systems.
“We want more than just a check on the food safety list,” Claude adds. “We want consumers to see food safety as who we are. Food safety is the cost of doing business.”
Warehouse Innovation: A Peek into the Future.
Randy Jennings, director of food and beverage sales at Swisslog, Newport News, Va., provided a short course on automation and how forklifts, automated storage retrieval systems and automated guided vehicles have revolutionized food distribution centers.
“Automation is not about taking away the operator,” Jennings says. “It’s about making him/her more effective. The use of technology is the have of tomorrow.”
Food Pathogens on the Move.
Jorge Hernandez, senior vice president of food safety and quality assurance for U.S. Foods, Inc., Rosemont, Ill., and John Kukoly, senior technical marketing consultant at BRC Global Standards, conferred about food safety risks in storage and distribution, and how sometimes food safety obstacles lie within the supply chain.
“Food transportation provides opportunities for threats of food safety,” Hernandez says.
Looking for a reprint of this article?
From high-res PDFs to custom plaques, order your copy today!