Ammonia Leaks: Prevent, Mitigate and be Prepared
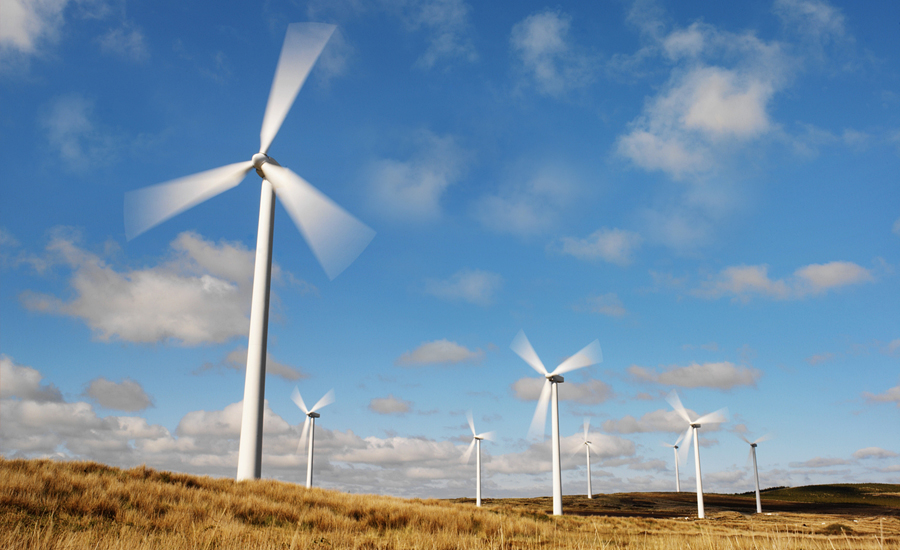
When the U.S. Chemical Safety Board (CSB), Washington, D.C., released a safety bulletin earlier this year informing companies that use anhydrous ammonia in bulk refrigeration operations how to avoid a hazard referred to as hydraulic shock, the cold food industry listened. In CSB’s investigation, it was determined that when designing ammonia refrigeration systems, each evaporator coil should be controlled by a separate set of valves. The CSB also discovered that an emergency shutdown should be activated in the event of an ammonia release if a leak cannot be promptly isolated and controlled.
That’s why organizations like the Ammonia Safety & Training Institute (ASTI), a non-profit organization based in Watsonville, Calif., works with the Refrigerating Engineers and Technicians Association (RETA), Albany, Ore.; International Institute of Ammonia Refrigeration (IIAR), Alexandria, Va.; and the International Association of Refrigerated Warehouses (IARW), an Alexandria, Va.-based partner of the Global Cold Chain Alliance (GCCA), to provide support and training on how to properly design, build and operate ammonia systems.
Here’s some insight as to how your company can prevent, mitigate and be prepared.
The meaning and value of PMP
Prevention-Mitigation-Preparedness (PMP) is a system that defines ways to manage any situation that presents risk to life, environment or property. The stronger the application of PMP, the less likely an ammonia release will occur. If an emergency event does occur, your team will be able to stop the problem when it is small.
Prevent problems through good housekeeping and systems upkeep. Establish team discipline to abide by standard operating procedures (SOPs) and maintenance protocols. Recognize that a clean and organized work environment reduces risk and improves efficiency and profitability of production.
Mitigate problems through engineering solutions, such as early warning for ammonia releases and fire. Install control systems to address specific threats before they materialize, e.g., solenoid valves that remotely control liquid flow to a release point and/or programmable logistics control systems that allow for containment and control operations while working outside the danger area. In some cases, mitigation is as easy as using proper signage. Your team will find innovative and cost-effective mitigations if you allow feedback when designing safer systems.
Prepare by training and equipping operators with proper personal protective equipment to safely perform maintenance and repair. Make sure the SOPs and emergency response plan are well understood and realistic. Develop response protocols that are easy to follow (pictorial) for emergency shutdown—don’t assume that one push of a button is sufficient for emergency shutdown. Develop pre-emergency readiness that engages the plant response team when risks and threats are highest, e.g., when opening the system for repair. Most importantly, integrate with public safety response by establishing a teaming agreement that clarifies conditions, actions and needs for industrial and public safety joint response coordination.
Pre-emergency training
The objective of the pre-emergency training is to assure that plant operators and contractors are properly prepared to work on the ammonia refrigeration system. Pre-emergency readiness gives the repair team an opportunity to stop a problem before it becomes an emergency event.
Many emergency releases start from a failed attempt to make a repair. The pre-emergency policy sets up the criteria for reviewing appropriate SOPs such as lock-out/tag-out, hot works permit, emergency shutdown and safe re-start. The policy also calls for the lead repair person to alert the plant incident commander prior to engaging pre-emergency status. A clipboard should display the check-off list of key readiness concerns, such as personal protective equipment, eye-level wind indictors, emergency shower readiness and radio and ammonia monitoring equipment to be used. The pre-emergency SOP also provides criteria for how to engage incidental control prior to declaring an emergency event.
The overall challenge to managing ammonia releases is to use PMP to reduce the risks and threats BEFORE the real-time concerns come to light.
Prevent, mitigate and be prepared.
Looking for a reprint of this article?
From high-res PDFs to custom plaques, order your copy today!